AC Motor Repair
HECO provides expert AC motor and AC generator repair services, restoring industrial units of all sizes. Our team specializes in rewinding, bearing replacements, shaft repairs, and electrical diagnostics, ensuring long-lasting performance for your AC motors and AC generators. With decades of experience and advanced testing capabilities, we deliver precision repairs that minimize downtime and extend motor life.
General Capabilities
- Electric motor and generator repair and rewinding
- AC motor testing capabilities of up to 13.8kV, 4000kVA
- Lathe machining capabilities up to 96-inch swing
- 10-foot diameter Vacuum Pressure Impregnation (VPI) system
- Clean winding rooms, the largest with 50-ton lifting capacity
- Von Roll Mica MAX Insulation system for up to 15kv+ VPI motors
- AC HiPot (High Potential Testing) up to 50 KV, 3.5 Amps
- Rotor Repair, including new bars and end rings or windings for Wound Rotor and Synchronous Motors
- Dynamometer testing up to (1,200HP) 4,400 foot-pounds
- EASA-accredited for electric motor and generator repairs
- Stator/Rotor design and manufacturing
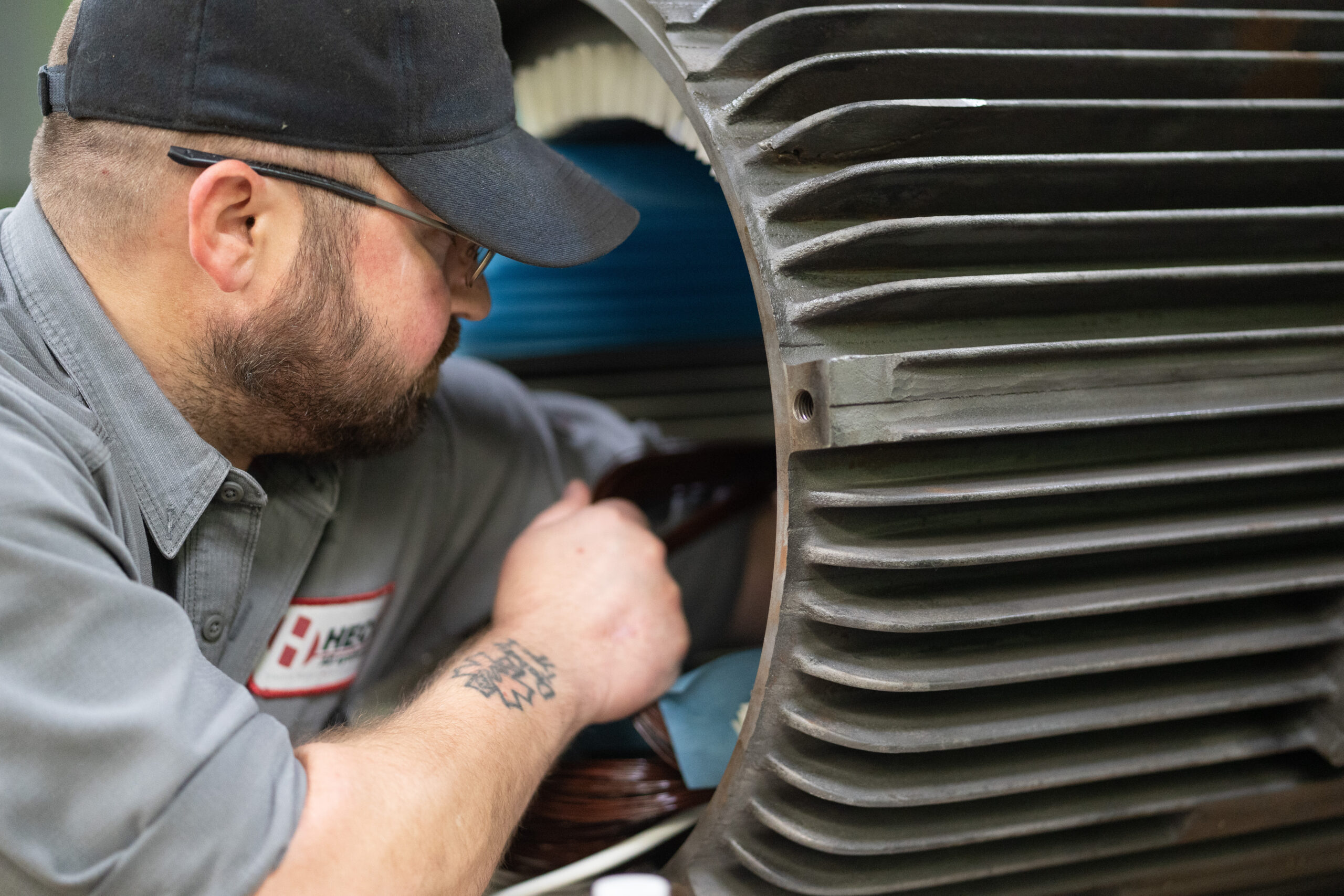
AC Synchronous Motors/Generators
AC Synchronous Motors/Generators
- Dimensional analysis and bracing assessment
- Coil insulation evaluation
- IEEE-standard electrical testing
- Temperature-controlled stripping of old windings
- Winding data analysis and potential design improvements
- Precision stator and rotor rewinding with integrity testing
- Evaluation of the existing insulation system
- Application of improved insulation for heat transfer and dielectric integrity
- Vacuum Pressure Impregnation (VPI) with solventless epoxy resin
- Rotor balancing and alignment correction
- Vibration spectrum analysis (FFT)
- Dynamic rotor balancing to correct imbalance
- Shaft alignment adjustments to prevent excess wear
- Root cause analysis for motor failures
- Identification of structural issues, misalignment, or imbalance
- Diagnosis of bearing defects, broken welds, loose fasteners, and rotor/stator faults
- Resonance condition analysis to prevent operational failures
- Design improvements for increased motor reliability
- Thermal management solutions to enhance longevity
- Application of best practices for energy-efficient operation
- Slip Ring Repair and replacement
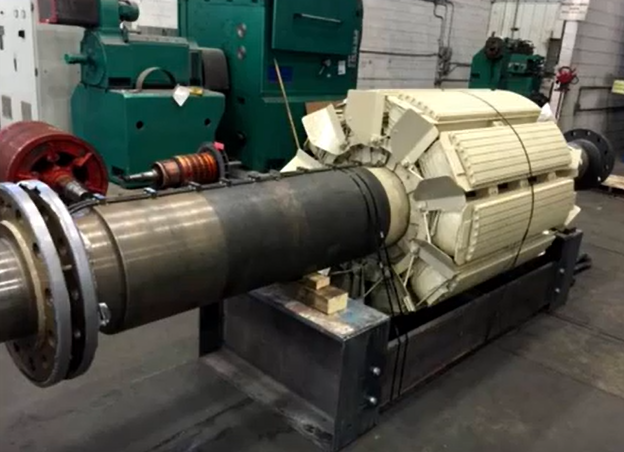
AC Slip Ring Motor/Wound Rotor Motor Repair
AC Slip Ring Motor/Wound Rotor Motor Repair
- Dimensional analysis and bracing assessment
- Coil insulation evaluation
- IEEE-standard electrical testing
- Temperature-controlled stripping of old windings
- Winding data analysis and potential design improvements
- Precision stator and rotor rewinding with integrity testing
- Evaluation of existing insulation system
- Application of improved insulation for heat transfer and dielectric integrity
- Vacuum Pressure Impregnation (VPI) with solventless epoxy resin
- Rotor balancing and alignment correction
- Vibration spectrum analysis (FFT)
- Dynamic rotor balancing to correct imbalance
- Shaft alignment adjustments to prevent excess wear
- Root cause analysis for motor failures
- Identification of structural issues, misalignment, or imbalance
- Diagnosis of bearing defects, broken welds, loose fasteners, and rotor/stator faults
- Resonance condition analysis to prevent operational failures
- Design improvements for increased motor reliability
- Thermal management solutions to enhance longevity
- Application of best practices for energy-efficient operation
- Slip Ring Repair and replacement
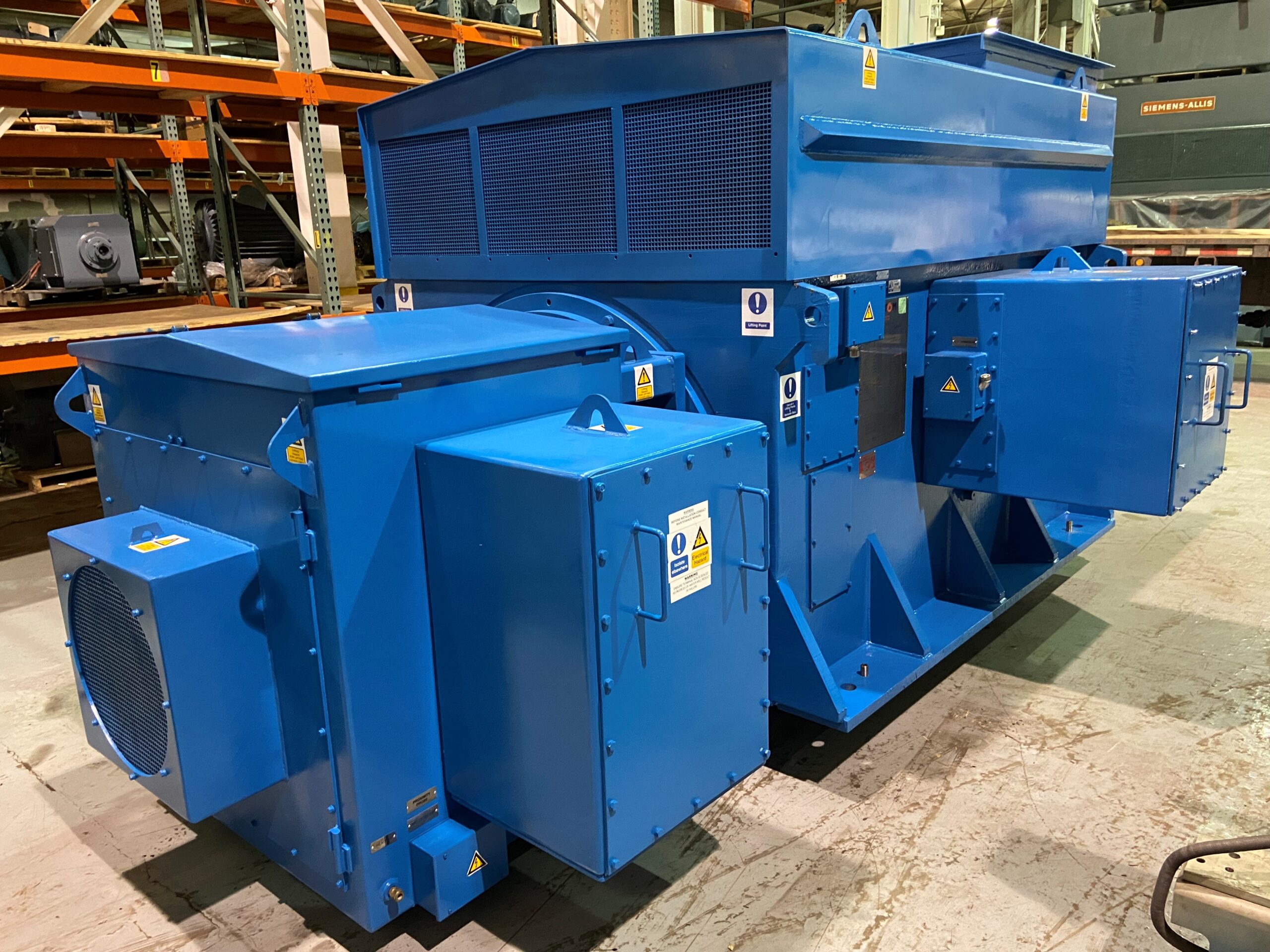
How a HECO Repair is Different
The way we think is what makes us and our repairs different. You’ll experience it with the first job when we ask you a variety of questions, such as:
- Why are you removing the unit? Did it fail?
- What is the application for your unit?
- How long has the unit been in service?
- What type of starting is used?
- Are there any special instructions?
Using these questions as a means to uncover the “why” of any issue you are having, HECO then focuses on potential issues to make the right repair on the first service and prevent the need for recurring repairs.
Learn more about how a HECO Repair is different.
Take A Virtual Tour
Want to see what kind of shop your motors will be going to? Check out a virtual tour of our Kalamazoo location.
Industries Served
The way HECO approaches electric motors, generators, pumps, gearboxes, and complete performance systems is tailored to your industry’s specific needs and characteristics. By asking “why” and incorporating the answers into specialized solutions, we are better equipped to find the right solution that will work for your industry.
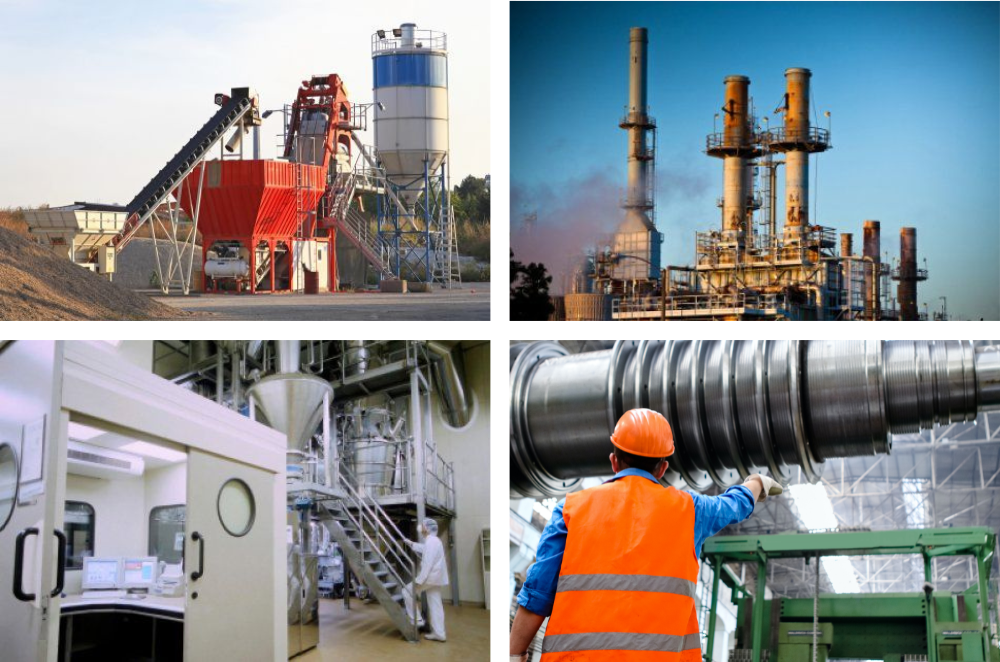
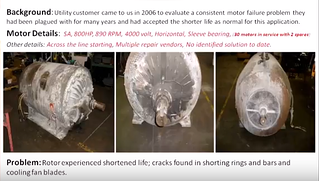
800HP Coal Crusher Electric Motor Repair Case Study
After years of repetitive failures, a Midwest-based coal-fired power generation plant turned to HECO for help in 2006. Recurring issues with an 800HP, 900RPM, 4000V coal crusher motor’s rotor needed our attention and unique approach to repair.
After diagnosing an issue with circulating currents from a variable frequency drive and electrical discharge damage, we implemented a custom grounding solution to eliminate the harmful currents.
By addressing the root cause, HECO significantly extended the motor’s lifespan and improved system reliability. As a result, the customer reduced unplanned downtime and maintenance costs, ensuring smoother operations.
This case study was originally presented at the Reliability, Process, and Maintenance (RPM) Symposium in September 2016.
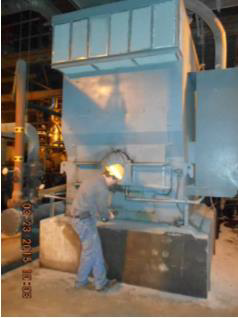
9000HP Boiler Feed Pump Motor Rotor Case Study
After bringing a coal-fired power generation plant’s 9000HP Siemens Allis Boiler Feed Pump Motor in for vibration analysis and noise concerns, HECO’s motor repair team uncovered severe contamination and structural damage.
The motor’s windings were packed with debris, its bearings showed signs of rust, and the shaft journals suffered oxidation-related damage. Additionally, clogged air filters prevented proper ventilation.
A deeper inspection revealed multiple hairline cracks in the rotor assembly’s bar-to-shorting ring joints, making repairs impossible. As a result, a full rotor cage replacement was proposed, reusing only the shaft spider assembly.
Read the full blog series dedicated to this case study, including:
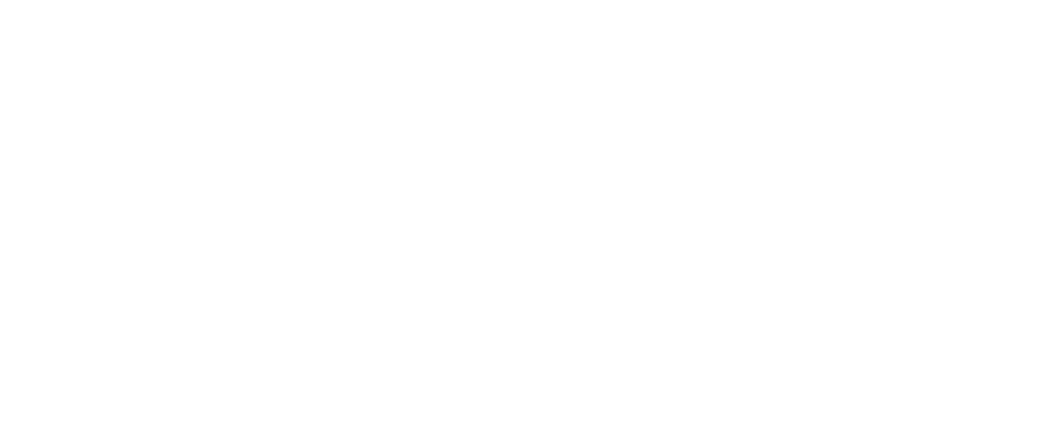