What is Cavitation & What Are the Causes of Cavitation? - HECO
March 1, 2022
Maybe you’ve got a centrifugal pump that sounds like it’s full of rocks, marbles, or gravel. That is a sign of cavitation — which can total your pump if you don’t track down the cause.
But what is cavitation anyway?
The official definition of cavitation is what occurs within a pump when the static pressure of the liquid drops below the vapor pressure of the liquid and bubbles (i.e., vapor-filled cavities) form. A more general definition would be the formation of bubbles within a pump, regardless of how they got there.
When these bubbles are exposed to high pressure, they begin to collapse, and that’s where problems start. As these bubbles collapse, they can generate tiny but powerful, high-energy shock waves that can damage components within the pump. The most damage occurs when the bubbles implode close to a surface — and in pumps that would be around the impeller.
What Causes Cavitation?
To understand what causes cavitation, you need to look at the different types of cavitation that can develop:
- Air aspiration
- Internal recirculation
- Turbulence
- Vane syndrome
- Vaporization
Air aspiration occurs when air is pulled into the system, becomes trapped, and bubbles form. These bubbles pop when they reach the impeller.
Internal recirculation occurs when the pump can’t discharge a liquid at the proper rate. This means the liquid re-circulates around the impeller, traveling through low- and high-pressure zones that lead to heat and high velocity — which produces problematic vaporized bubbles that will begin to pop.
Turbulence occurs when vortices develop within the liquid. As the liquid becomes turbulent, pressure differences are created and problematic cavitation bubbles form. Turbulence can result when you exceed the performance guidelines for the pump, or the pump suction line is too small.
Vane syndrome usually results from one of two things: either the diameter of the impeller is too large, or the housing has a coating that is too thick. Either way, there isn’t enough space within the housing, and liquid passing through it reaches a higher velocity than the pump was designed for. The higher velocity leads to a lower pressure that heats the liquid, and destructive bubbles result.
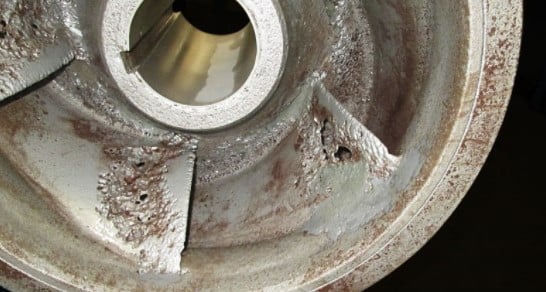
Vaporization matches the official definition of cavitation. It is the most common type and is often called “Classic Cavitation.” A centrifugal pump essentially spins a liquid as it passes through the eye of the impeller. And the liquid may reach its boiling point if the impeller isn’t working right, leading to vaporized cavitation bubbles. This happens when the pump’s minimum energy requirement (the NPSHr) is higher than the available energy in the system (the NPSHa).
How Do I Prevent Cavitation?
So, given these definitions, how can we prevent cavitation?
Air Aspiration Cavitation
Anywhere the pump is in a vacuum state is a potential source of air aspiration, which makes for quite a list. To prevent air aspiration, start by searching for anywhere air might be sucked into the system. Inspecting pipes for cracks or erosion is essential, and so is checking o-rings and secondary mechanical seals for wear.
You can also check to see if the foaming liquid leads to the formation of air bubbles. Any liquid that can foam can also introduce air into the pump. If you have a foaming liquid, you can slow the pump RPM or occasionally empty the liquid. Something else you can do is ensure that the fluid being pumped isn’t causing the piping or pump to deteriorate and allow air in.
Internal Recirculation Cavitation
Internal re-circulation commonly occurs when a discharge valve remains closed while the pump is in operation. There are two basic things you can do to prevent internal recirculation cavitation:
- Ensure that the discharge valve (1) is open and not closed and (2) hasn’t been installed backward
- Check any downstream filter to be sure it is not clogged
Turbulence Cavitation
Pipes, elbows, and valves may not be adequate for the amount of liquid you’re pumping, which can create vortexes, pressure differences, and turbulence. Here’s what you can do to prevent turbulence and the caviation is causes:
- Don’t exceed the maximum allowed flow limit of your pump
- Maker sure all the components can withstand the strain of the pumped liquid
- Try to avoid turbulence in the pump suction line, including how you size it and how you route it
Vane Syndrome Cavitation
Vane syndrome cavitation can be prevented by following this rule: the free space between the housing and the impeller blade tips should be at least 4% of the impeller diameter. Anything less than this will cause cavitation.
Vaporization
To start with, here is a good rule of thumb for preventing cavitation due to vaporization: NPSHa > NPSHr + 3 ft. This heuristic creates a good safety margin, and if you can’t achieve it, consider replacing the pump, such as using two lower capacity pumps in parallel instead of just a single pump. Another option would be to use a booster pump to remove the stress from your primary pump.
Another approach would be increasing the liquid level around the suction area. Other possibilities include reducing the RPM of the motor, which will reduce the head pressure and flow rate. And if possible, try lowering the pump’s temperature and the liquid.
Conclusion: Preventing Cavitation is Critical for a Healthy Pump
By preventing cavitation, you will significantly increase your pump’s efficiency and lifespan. Keep an eye on the impeller for signs of pitting and corrosion. And listen to the pump to ensure you don’t hear what sounds like marbles banging around.
At HECO, we can help you address all your pump problems, from maintenance to repairs. If you are having cavitation issues, contact us today and learn how HECO can help you!
Posted in Predictive, Repair