Repair
Whether you need help to repair a motor, pump, gearbox, or fan/blower, HECO has the services you need.
Our shop equipment doesn’t make us successful; the strict procedures HECO has followed since 1959 do. Our philosophy and approach are what make us and our repairs different.
You’ll experience the difference with the first job when we ask you a variety of questions before we pick up the unit, including:
- Why are you removing the unit? Did it fail?
- What is the application for your unit?
- How long has the unit been in service?
- What type of motor starting is used?
- Do you have a repair specification that we need to adhere to?
Using these questions as a means to uncover the “why” of any issue you are having, HECO then focuses on potential issues to make the right repair on the first service.
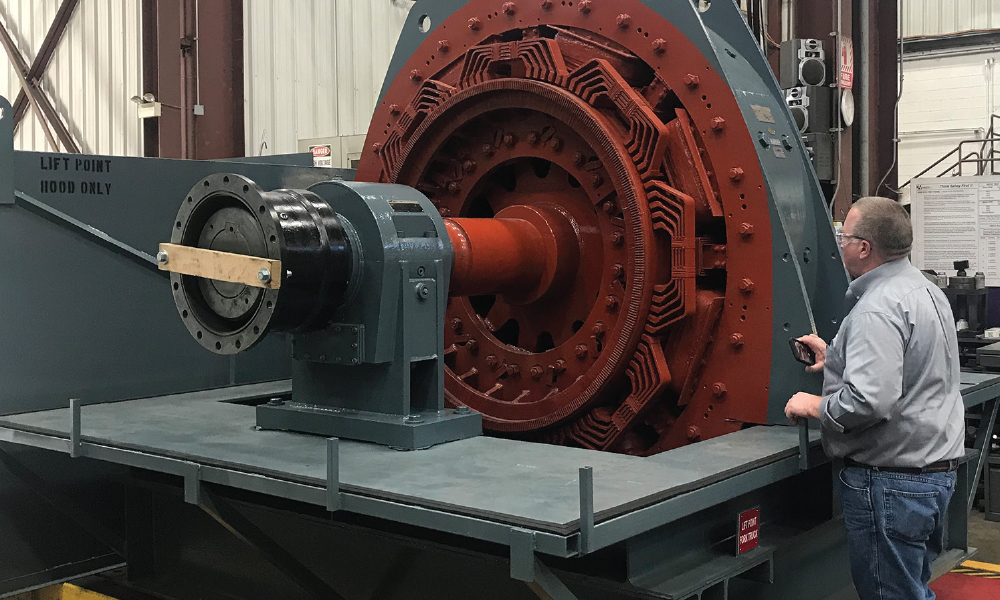
Equipment We Repair
How We Do It Different
HECO goes well above and beyond in our step-by-step approach and included deliverables.
1. Repair Procedures/Documentation
Our procedures and forms are one-of-a-kind. They are put together for each different motor type: AC ball bearing, AC sleeve bearing, DC ball bearing, AC synchronous, AC vertical, etc.
Based on the specific motor in question, different procedures must be followed and different tests are required – hardly any of which are simply pass or fail. HECO records the results of each test for future comparison or customer review.
We invite you to come take a look at our testing procedures and compare them to others. At HECO, we have nothing to hide – it’s all right there for your review and documented for the future.
2. Bake-out Time for Moisture
A motor must be cleaned during the repair process to remove any and all contaminants. Then, it must be baked out to remove any residual moisture. While many “rules of thumb” are used to determine how long a motor should be baked, it is critical to consider how long it takes the middle of that mass to come up to a temperature that removes the moisture. HECO factors that in.
Using precise temperature probes, we ensure that the middle of the mass has come up to temperature and that all the moisture has been removed. Without this process, you could be varnishing over the top of moisture and trapping it within the motor. This could lead to a premature failure, so we take steps to ensure all moisture is removed.
Your motor may need to bake out for a longer period – sometimes several days – but this thoroughness assures you that the repair process is being performed correctly.
3. VPI Processing Times
We perform many rewinds on low, medium, and high voltage motors. HECO was also one of the first EASA shops to install a vacuum pressure impregnation (VPI) system when only the manufacturers had them. We didn’t just get a VPI tank to be competitive, we got it because we understand the benefits of a void-free insulation system.
Each motor that goes through our VPI system is different; the coil design is different, and the layers of tape on the coils are different. So instead of just following industry “rules of thumb” for how long to process the VPI, we calculate the time it will take for full penetration. On top of that, we send a sample coil through with each process we run. We then cut the coil in half before curing the resin to ensure the process went per our calculations.
You’re left with a verifiable, void-free winding that will ensure the longevity of your winding and insulation system.
4. Magnetism in Shafts
With the rise of variable frequency drives (VFDs) and other factors, circulating currents have become more common, leading to mechanical component failures. These currents not only damage bearings directly but also generate magnetism in the motor shaft, increasing the risk of future failures.
HECO checks magnetism on every motor we have in-house and even has the correct equipment to remove this magnetism from the mechanical components. Simply installing a shaft grounding device, such as an AEGIS Shaft Grounding Ring, does not remove magnetism that has already been created from the currents; it only prevents it from happening again. So we remove the magnetism, essentially fixing one of the results of the currents, and install an AEGIS ring to prevent it from happening again.
The result is mechanical components that have been wiped of the problems these currents can cause with a device that will protect from the currents in the future, creating a one-of-a-kind solution from HECO.
5. What Versus Why – The Most Important Difference of All
Our industry has a standard for “what” companies. When a motor fails, the repair shop asks “What is it? I’ll come pick it up.”
These shops can do a great job and can generally get the customer out of a bad situation quickly. However, using a “what” mindset shop can become frustrating. Failures can keep recurring with no solution in place to stop them. These shops can do a great reactionary job and can work around the clock to get that motor back to you, but the motor keeps failing and you keep having downtime.
The difference is that HECO is the “why” company. Using the above example, the fault lies in never stopping to ask, “Why did the motor fail in the first place?” or “Why don’t you have a spare so your plant can keep running despite the failure?”
We want to help you become proactive and fix something correctly the first time.
Let’s be realistic, we cannot always understand what took place from looking at just the motor. We have to ask our customers questions in order to learn the events that took place leading up to the failure and the history of the machine so we can perform a true root-cause analysis. If we looked at just the motor, we could just be looking at the result of a failure, not what actually caused it.
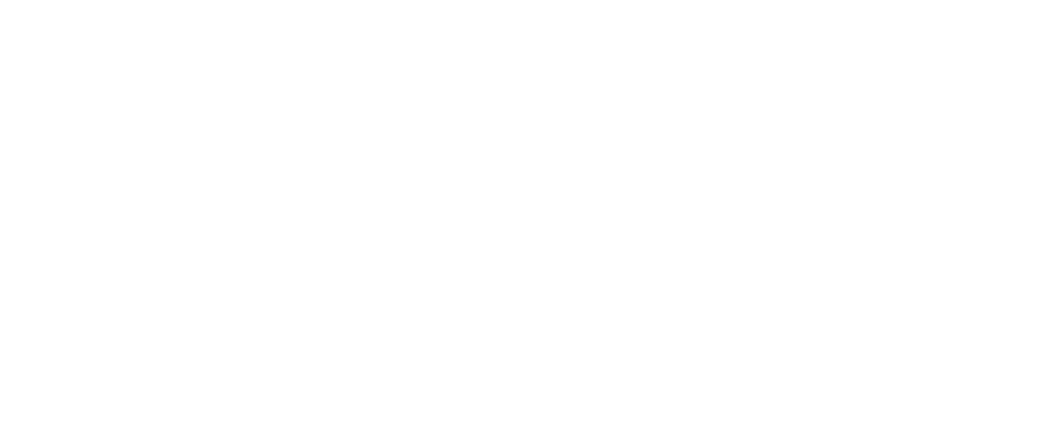